Wave-Core™ Helps Glass Manufacturer Reduce Operational Costs
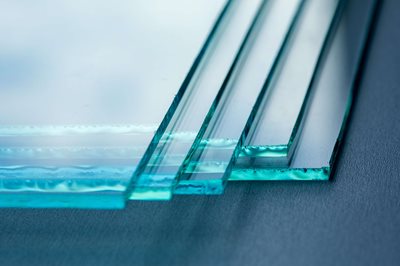
Project Overview
When a glass manufacturer experienced rising operational costs due to a production inefficiency, Wave-Core™ corrugated plastic helped lower this escalating cost. The manufacturer needed a durable, easy-to-ship solution that would replace their fiberboard materials without adhering to uncured silicone. Not only did Wave-Core™ resolve the issue, but our proprietary solution helped the manufacturer see tangible business results.
Challenge
Despite multiple attempts to stage assemblies on fiberboard, the compound still caused additional cleanup costs, customer complaints, replacement costs, and delays. The manufacturer needed a solution that could:- Replace problematic fiberboard material with a non-adhesive material
- Withstand warehouse handling and transport
- Be reused for closed-loop manufacturing
- Be customized for dimensions and load weights
Solution
The team used Wave-Core™ corrugated plastic to replace the problematic fiberboard material. The solution, an extruded single face, was cut into custom-sized strips and conditioned with a surface treatment to meet the customer’s adhesion requirements. Treating the pieces allowed the glass to be successfully stacked and fully cured without the silicon adhering to the board during transport. The durability of Wave-Core™ corrugated plastic ensured a stress-free handling process and a reusable closed-loop solution.
he Wave-Core™ team:
- Replaced fiberboard with HDPE plastic
- Prevented the silicone compound from adhering to glass material
- Improved operational efficiencies and costs
Services Provided
- Warehouse stocking program
- Customized to meet manufacturers specifications
- Easy-to-handle protective strips
- 100% recyclable
- 100% reusable packaging
Download Case Study